
At Bossard, we believe that our holistic view, Proven Productivity, is key to getting ahead with you, through developing solutions that are more efficient and cost-effective.
In the wake of modern industrial changes, thinner and lighter components such as metal plates, PC boards or plastic pieces are increasingly used due to ever growing demands from consumers. While trying to achieve secure assemblies with high torqueout and pull-out performance, manufacturers are also looking into ways to simplify the process and ensuring cost savings. A great way is looking into the design phase of the assembly by reducing the number of fasteners required, leading to fewer process steps in the final assembly. Self-clinching solutions ensure secure assemblies while being easy to install. This leads to cost savings due to reduced fasteners cost as well as shorter assembly times.
Bossard portfolio of self-clinching & piercing solutions are able to meet the different industrial requirements. From thin sheet metal to heavy duty applications, our range of product solutions allow us to meet individual customers’ requirements. Using our broad portfolio and technical expertise, we support our customers from design to mass production, reducing costs and increasing competitiveness. Listed below are some of our product solutions. The product images shown are for illustration purposes only.
To find out more about our product solutions, do contact us at pd.asiapacific@bossard.com
Products
Self-clinching Nuts & Studs
- High torque-out and push-out resistance
- Thread-locking and self-locking for assemblies exposed to dynamic loads and vibrations
- Floating functionality to compensate mating hole misalignment
Self-broaching Standoffs
- Electroplating to promote solderability for PC boards
- Suitable for non-ductile materials
- High torque-to-turn resistance and pull-out performance
Fastener Insertion Machines
- Fully hydraulic mechanics and modular equipment based on your needs
- Single-touch technology for precise and process reliable instalment
- Automated and customized solutions for process cost reduction
Product Solutions for the EV Charger
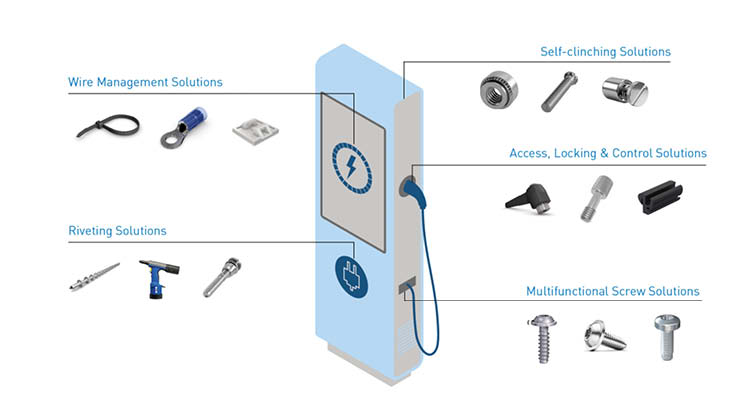
The customer is engaged in the development and manufacturing of telecommunication and electronic technology products such as Electric Vehicle (EV) chargers
Customer Pain Points
- Customer is facing challenges relating to unsightly weld marks (aesthetic concerns) and distortion to the sheet metal during welding of Studs.
Opportunity
- Bossard was consulted to propose a solution to improve aesthetics of the assembly.
- Self-Clinching Technology is a good alternative to welding of such assembly in metal fabrication application and it offers cleanness and improved aesthetics.
Action
- Self-Clinching studs on sample plates were shown and demonstrated to the customer, who appreciated that the panel surface is flush and free of unsightly marks.
- A trial was conducted at production site with proposed Self-Clinching Stainless-Steel Studs with successful results.
What are the benefits ?
- The process is faster and cleaner using this Self-Clinching Technology as compared with Welding Technology for this application.
- Self-Clinching Technology utilizes clean energy which comes from compressed air compared to Welding Technology which run on electric power.