Corrosion Protection
Download
Galvanic process - fasteners with electroplated coatings (according to ISO 4042)
based on chromium (VI) for the corrosion protection of fasteners. Today the use of chromium (VI) coating is restricted. For this reason, for new applications it is recommended to use only Cr(VI)-free conversion coatings (passivation). The surface treatments based on chromium (VI) – free systems usually require a more complex process control since the so called «selfhealing effect» is less pronounced. Bulk handling, automatic processes such as feeding and / or sorting, storage and transport can cause a reduction of the corrosion protection (especially protection against corrosion of the coating) depending on the coating system and the type and geometry of the fasteners.
Guiding values of the corrosion resistance for commonly used zinc and zinc alloy coating systems according to ISO 4042:2018
Possible tolerance adjustments for surface coatings ISO 10684 (hot galvanization)

Reference areas for coating thickness determination
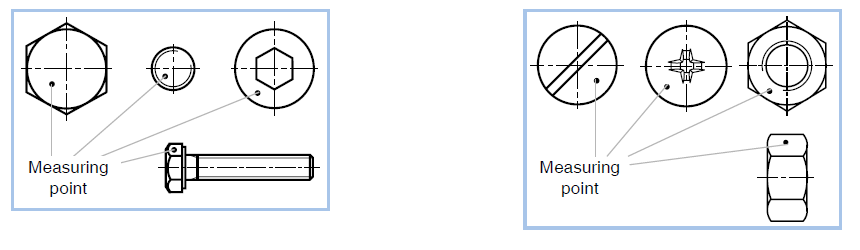
Further galvanic coating processes
Process | Details |
Nickel-Plating | Nickel-plating is decorative and provides effective corrosion protection. A hard coating, used in the electrical appliance and telecommunications industries. No coating abrasion occurs, especially with screws. Improves protection against impregnation, see table below. |
Veralisation (Thick layer nickel plating) |
Is a galvanic (electrochemical) nickel coating ideally suited for workpieces subjected to heavy loads. |
Chromium-plating | Usually following nickel-plating. Coating thickness about 0,5 – 1,0 μm. Chromium is decorative, enhances resistance to tarnishing and also serves as corrosion protection. Bright chromium-plated: high brightness finish. Matt chromium-plated: matt lustre (silk finish). Drum chromium plating not possible. Creates a hard surface with good wear and sliding properties. |
Brass-plating | Brass plating is mainly applied for decorative purposes. In addition, steel components are brass-plated in order to improve the adhesion of rubber to steel. |
Copper-plating | As primer prior to nickel-plating, chrome-plating, and silver-plating as needed. Used for decorative purposes. |
Silver-plating | Silver-plating is employed for decorative and technical applications. |
Tin-plating | Tin-plating is carried out mainly to permit or improve soldering (soft-solder). Simultaneously serves as corrosion protection. Subsequent heat treatment not possible. |
Anodizing | When aluminum is anodized (electrolytic oxidation), a coating which provides corrosion protection is produced – also prevents tarnishing. Practically any color can be produced for decorative purposes in a downstream coloring process. |
Zinc / iron alloy coating |
Is a galvanic coating process which uses an electrolyte that precipitates a zinc-iron alloy on a metallic component. Following the coating a Cr(VI)-free black passivation and black sealing is applied. It is mainly used when a cosmetic black surface is desired. |
Zinc / nickel alloy coating |
The zinc-nickel coatings have a deposition of approximately 12 – 16 % share of nickel during the galvanization. Here one has the possibility to use a transparent or black passivation and to optimize by a sealing. This coating is mainly used because of its good corrosion protection in use. |
Further surface treatments
Process | Details |
Hot-dip galvanizing | Immersion in molten zinc with a temp. of about 440 °C to 470 °C. Thickness of coating not less than 40 μm. Finish dull and rough. Color change possible after a certain time. Very good corrosion protection. Can be used for thread parts from M8. Threads need to be over or undercut to assure proper thread mating. |
Zinc flake coatings Geomet® Delta-Tone® / Delta-Protekt® |
Zinc flake coatings are excellent for high strength components with tensile strength of Rm ≥ 1000 N/mm2 (Property class ≥ 10.9, Hardness ≥ 320 HV). This process practically eliminates the possibility of hydrogen embrittlement. Temperature resistant 300 °C. Can be applied to size M4 and up. |
Mechanical plating | Mechanical / chemical process. The degreased parts are placed in a drum with powdered zinc and glass pellets. The pellets serve to transfer the zinc powder to the surface to be treated. |
Black oxidizing of Stainless steel |
Chemical process in hot hydroxide solution. For decorative purposes. |
Black oxidizing | Chemical process, bath temperature about 140 °C. For decorative purposes. Temporary corrosion protection only. |
Phosphate (bonderizing, parkerizing, atramentizing) |
Only slight corrosion protection. Good undercoat for painting. Grey to grey-black appearance. Better corrosion protection oiled. |
Waterproofing / sealing | Particularly with nickel-plated parts, subsequent treatment in dewatering fluid with the addition of wax may seal the micropores with wax. Significantly improves the corrosion resistance. The wax film is dry and invisible. |
Baking | Following electrolytic or pickling treatment, high tensile strength steel parts (from Rm ≥ 1000 N/mm2, corresponding to ≥ 320 HV) can become brittle due to hydrogen absorption (hydrogen embrittlement). This embrittlement increases for components with small cross sections. Part of the hydrogen can be eliminated by baking between 180 °C and 230 °C (below tempering temperature). Experience indicates that this is not guaranteed 100%. Baking for >4 hrs must immediately be carried out after pickling and after galvanic treatment. |
Sealing | Sealing is applied to the component using an immersion process after galvanization and passivation. Sealing increases corrosion resistance. |
Tribological dry coating1) |
These coatings provide a friction reducing and wear resistant film. Reduce galling tendency. |
Waxing | Provide a lubrication layer, reduces driving torque of thread-forming screws. |
WIROX® | Is a galvanic coating with zinc, average thickness at least 8 μm. The corrosion protection is more than 20 times higher, compared with plain galvanizing. The coating is resistant to abrasion, mechanical loads and is characterized by an exceptionally high corrosion resistance. |
YELLOX® | Is a galvanic coating with zinc, average thickness at least 4 μm. The corrosion protection is more than 6 times higher, compared with plain galvanizing. Screw applications with yellowish appearance are guaranteed in the future. |
GreenTec® | Is a galvanic coating, thickness about 5 μm, zinc-nickel-based and provides hard, wear-resistant coating with very high corrosion resistance. |
1) For example CresaCoat®
CresaCoat® tribological dry coating is a non-electrolytically applied, thin layered coating with integrated lubricating properties and additional corrosion protection. The coating consists of a composition of fluoropolymers and organic submicroscopic solid lubricant particles, which are dispersed in carefully selected synthetic resin blends and solvents. The AFC coating (Anti-Friction-Coating) creates a smooth film, which balances all unevenness of the surface thereby optimising friction under extreme loads and working conditions. The synthectic resin in turn ensures better corrosion protection.