Questioning the process of welding
SEMAT Zoeller, a manufacturer of trash trucks and vehicles for city cleaning, has been a long-time partner of Bossard France SAS. Recently, they have questioned certain fundamental design choices of their products in response to the ever-greater challenges of our time, such as flexibility and productivity.
What they were scrutinizing, in particular, was the demanding process of welding. The structural elements of the bases of trash trucks had previously always been assembled by welding. However, this is a skill which is becoming increasingly rare and was subject to many constraints that slowed down their industrial manufacturing.
Rivet technology as an alternative
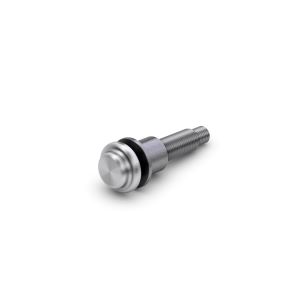
Bossard assisted SEMAT Zoeller in this process, suggesting an alternative solution: riveting. This would help our customer achieve greater flexibility in their organization as well as to simplify processes, thereby achieving an optimal assembly performance.
The structural Huck riveting solution that we proposed is quick, repeatable, and extremely durable even in the toughest of environments, such as against shocks or corrosion. This solution also meets the customer requirement of ease of use. In fact, it is easy to attach the rivets, even when you are dealing with hard-to-reach places under the truck's chassis. In addition, training time for workers is very short, unlike that of a welder, which takes years to learn.
Support in finding the optimal solution
After examining the customer's specifications, we proposed the Huck BobTail® rivet bar/ring method. Their very high resistance to shearing and the simple design make them the best-suited method for the application.
We then accompanied SEMAT Zoeller in implementing prototype assemblies to validate accessibility by the machines, suitability of the equipment for the industrial environment of production sites and to subject the assemblies to the required performance tests.
Decisive for finding the optimal technical solution here was our deep product knowledge, enabling us to consider our customer's professional constraints, the rules of their environment, as well as the problems of hard-to-reach places.