Entering Industry 4.0? Get an Employee Re-Training and Recruiting Plan
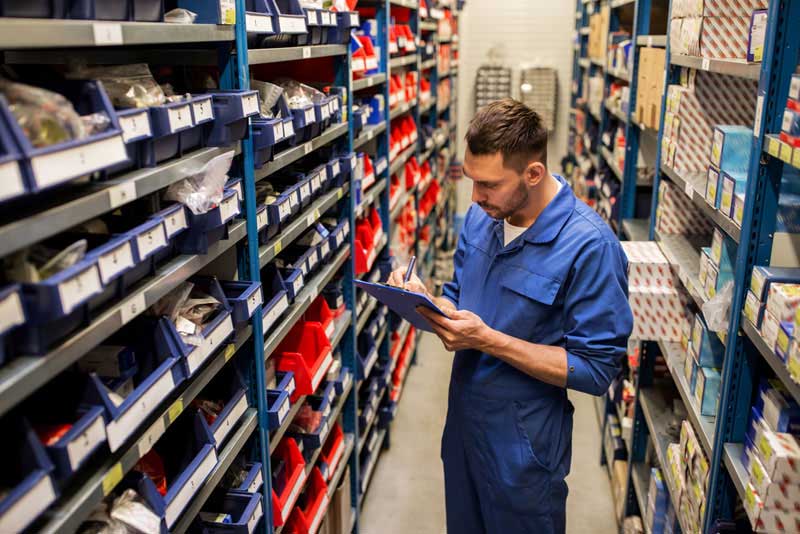
Digitalization isn’t all about robots. In fact, it has the ability to create MORE employment! It’s possible to create an excellent Smart Factory full of knowledgeable and successful human employees, without a robot in sight.
You can make enormous improvements in your operations and manufacturing processes by harnessing the capabilities of your current employees and re-training them to help them adapt to the changing workplace. You’ll probably have to hire workers with new skillsets as well.
Re-training Current Employees for Industry 4.0
Retaining your current talent should be a priority. There is a lot you can do with the workforce you already have.
It’s often said that one of the barriers to implementation is skill. Your current workers may not have all the skills needed to operate a digitalized factory, but they do know a lot about your factory already. Even if a complete overhaul to your operations and manufacturing processes is in order, your current employees have a significant advantage, especially if you’re able to teach the necessary skills and efficiently adapt them to the new processes.
Reassure your workforce that digitalization does not have to mean job loss. Instead, focus on changing internal processes. Train employees in new methods and technologies. Retraining your workforce is no small task, but the long-term benefits outweigh the costs.
Sometimes, you can optimize your factories and implement Industry 4.0 technologies without re-training anybody! Bossard Smart Factory Logistics is one of many ways to digitalize your factory in a way that your current workers will easily understand. For example, when you replace your bins with Bossard SmartBins, there is absolutely no learning curve required for employees (other than the fact that they have less to worry about!), but your factory is that much smarter.
Sourcing New Talent with Digital Expertise
Not everything can be taught in onsite training, and you will have to hire new talent at some point in the process of digitalization. As Industry 4.0 spreads across the globe, manufacturers will need to attract the right talent and find new employees with education and skills relevant to new and upcoming skillsets.
This might require a shift in recruiters’ mindsets: instead of determining whether new talent is qualified by looking at degrees and certificates, hiring managers will need to look for flexible, adaptable employees who are willing to succeed no matter what new technologies emerge around the corner.
Many young graduates have been brought up with this mindset, and they’ll find it easy to adapt to whatever comes next. Find new talent that has the skills and flexibility, and they will be a great resource as you attempt to build flexibility and adaptability into your Industry 4.0 business model.
Learn more about how you can get ready for Industry 4.0 and Digitalization in the E-Book 7 Steps to Get Ready for Industry 4.0 / Digitalization (Without Robots).