The Expert Team puts together their know-how and application experience in fastening especially for you. Have a look at these interesting white papers.
We help you master the science of fastening
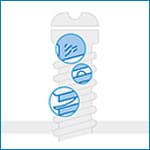
7 tips to select your fastener finish
Surface treatment plays a significant role in choosing the right fasteners. This white paper will investigate the six most-used coatings (zinc electroplating, zinc/nickel plating, mechanical zinc plating, zinc flake coating, hot dip galvanizing and epoxy coating) using seven criteria.
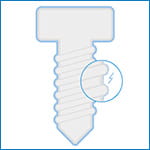
Common platings and coatings for fasteners and how they perform
For fasteners, a wide range of materials are available for use in various environments, and many more types of platings and coatings are available as finishes where needed. The right solution for any situation is ultimately defined by technical and economic considerations, and there is no solution which fits every situation.
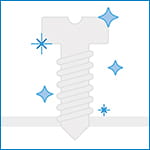
Importance of surface finish in stainless steel
This white paper will show the importance of passivation, polishing medium and surface profile on the corrosion resistance of stainless steel. In addition, it will also demonstrate the importance in obtaining a correct specification of architectural features where cosmetic appearance is a dominant factor.

The notion of "appearance" in coatings
Corrosion-resistance, strength, stability. In addition to these classic properties of mechanical connections, often an additional aspect plays an important role: Aesthetics.

7 criteria to prevent material fatigue
Material fatigue is defined as an accumulating degradation of material caused by dynamic stress with amplitude below the tensile strength limit. Considering the possible danger which material fatigue represents, design engineers should pay a lot of attention to every single aspect related to dynamic loads. This white paper will show how a design engineer should decide when dynamic loads are expected and which criteria the fastener or any other part should meet.
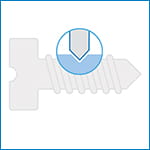
Hardness measuring techniques and the application at fasteners
The subject of hardness and hardness measurement practice is, simply said, a mature technology. This paper will provide a glimpse of the prevailing practices in the fastener industry and share the experiences in the hope that the use of material hardness results will be used in an appropriate manner.
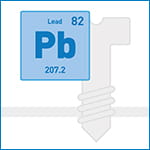
The usage of lead as addition to metals and its consequences
The purpose of this white paper is to provide information on the usage of lead as addition to various metals as well as the alternatives and their consequences. Together with information about the requirements of applicable industrial standards, it is intended to display the current situation on the market.
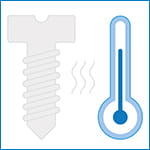
Which fasteners need a heat treatment?
Heat treatments allow, on the one hand, only certain processing methods for materials. On the other hand, they are used to increase mechanical strength (ductility) and, for some alloys, corrosion resistance. In this white paper, you will learn about important facts on heat treatment of steels as well as aluminium and non-ferrous alloys, their classification and their relevant mechanical characteristics.

Why friction in screw connections is crucial for process capability
«Lean Production» is the current trend and represents even leaner and more target-oriented processes. Solutions for higher efficiency, lower consumption and longer service lives are being researched worldwide. When assessing new materials or processes for surface treatment or finishing, tribological properties such as friction, lubrication and wear are almost always a factor.
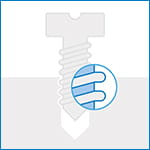
DIN 7500 – the first choice fastener for many situations
The DIN 7500 standard was first published in the late seventies and has been updated a number of times since. Simultaneously with the publication of DIN 7500-2 “guideline values for hole diameters” the standard for screws was named DIN 7500-1. However, most often the screws are just referred to as DIN 7500. Discover the reason why DIN 7500 screws have greatly increased in popularity over the years and continue to be the first choice fastener for many situations.
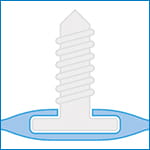
The challenge to find the right fastener solution for composites
As composite materials grow both in range and volume of applications, the challenge to find the right fastening solution continues to grow. This white paper explores some trusted fastening solutions within this fast growing market.
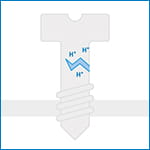
Hydrogen embrittlement - the silent killer
The embrittlement of metal caused by hydrogen atoms is not new. It was first reported back in 1875, more than a century ago. Nonetheless the awareness of the risk of hydrogen embrittlement, especially in mechanical fasteners deserves more serious attention.
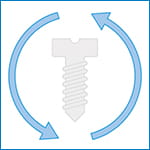
Should fasteners be reused?
The reuse of screws, nuts and bolts sounds as though it should save costs, but it does not. In this white paper, Martin Rüedy from the Bossard Expert team does not recommend the reuse of fastening elements in relation to five different factors.

What is corrosion?
Corrosion can occur whenever different metal components are in contact each other. What immediately comes in mind when we hear about corrosion, is the brown-reddish piece of metal. When we ask the expert, the answer is not quite as simple. Corrosion can be in different colors and forms. So what really is corrosion? What causes it? How to avoid it?
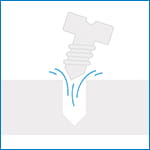
Loosening joint - don't lose it!
We have all experienced it. Screws or nuts are loosening – whether on a bicycle or on a pair of glasses. So, what is the cause of this? And how do we prevent this?
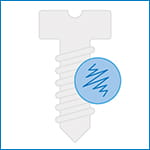
Galling of stainless steel fasteners
Are your connecting components regularly subject to seizing and so frequently cause a problem? In this professional article you can not only learn the causes and preventative measures, but targeted solutions for preventing cold welding.
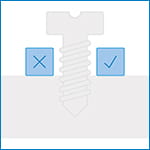
Choosing the right fastener at the design stage
Selecting the appropriate fasteners is closely linked to a well-defined fastener strategy and can prove beneficial in numerous ways in the long term. Making intelligent decisions from the very outset not only ensures both the quality and the efficiency of your design, but also leads to savings in manufacturing and process costs. In this whitepaper, we aim to strike a balance by addressing both product design practices and the decision-making process for fastener selection. The focus is on enhancing productivity while minimizing associated risks.
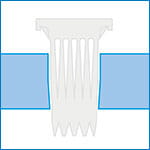
Artificial Intelligence and Big Data: Real-time quality control of joining processes
How can machine learning be optimally applied in lightweight construction? With its software SmartSolutions, MultiMaterial-Welding offers a first approach to the digitalization and quality control of joining processes. This white paper provides you with comprehensive insights into the connection technology platform.
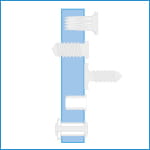
Fastening solutions for composite and plastic materials
Composite and plastics are go-to materials in many applications; designers and engineers seek innovative fastening solutions for them. In this white paper, you will learn about available technologies and different options for creating solutions.